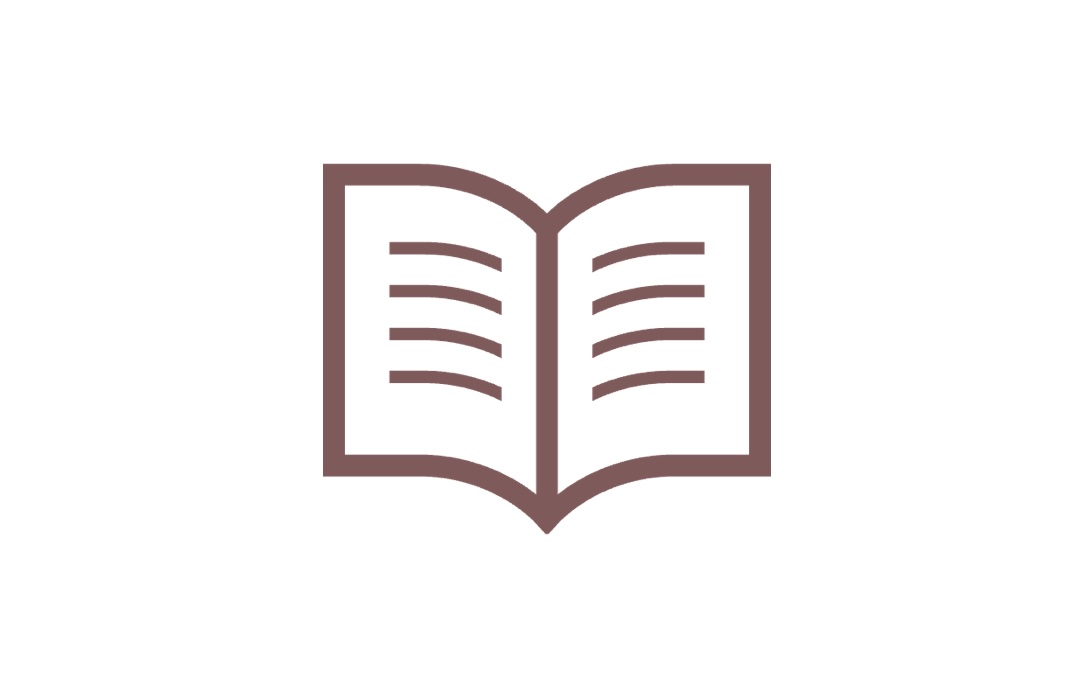
ご希望の方は「カゴに入れる」ボタンをクリックしてください。
仕様平準化VE
仕様平準化VE
株式会社日立製作所清水工場企画室 VAグループ:中村雅彦
近年の低成長経済下では,軽量経営の一環として,製品,部品,材料など在庫量を極力圧縮することが要求される。一方,市場ニーズの多様化,新分野への参入など,製品機種は増加の一途をたどり,在庫量の圧縮の妨げとなっている。この打解策として「かんばん方式」による小ロット生産などと並び,「部品の標準化活動」が非常に有効である。
しかし,一般傾向として,各製造業種とも,「標準化」の必要性は十分認識しながら,実際には顕著な推進がはかられていない。その理由としては,各企業の体質,環境にもよるが,次の要因が考えられる。
1) 製品シリーズ毎のモデルチェンジ頻度が異なり,部品の仕様格差が大きい。
多くの製品シリーズ群のうち,特に同業他社とのきびしい競合下にある製品シリーズは,モデルチェンジの頻度が激しく,より価値ある新部品が要求され,採り入れられる。一方,それ以外の製品シリーズは,とり残された形となり,同一機能部品でも仕様,コストなど著しい格差が生ずる。したがって
(a) 仕様の統合が困難で,標準化としてまとまりにくい。
(b) 標準化案を立案しても,取付寸法が異なるなど,手数がかかり,切替手配段階で敬遠される。
2) 標準化案に魅力(コスト面,仕様面)が無い。
1)で記すような条件下で,互換性を考慮し過ぎた場合,既存部品ベースでの「最大公約数的仕様」になり易く,将来構想に欠け,ややもすれば価値が低く,寿命の短かい標準化案(標準部品)となってしまう。
3) 設計者の個人差によるもの。
設計者の個人差によるものとして,
(a) 設計者の好みの差(形,デザイン,方式)が,部品仕様に反映され易い。
(b) 法規制を受ける製品については,関連法規の解釈に微妙な差異があり,部品使様に反映され易い。
(c) 信頼性,安全に対する解釈度の相違,データの不足が部品仕様に左右され易い。
(d) 顧客ニーズのとらえ方に差が生じ易い。
4) 推進体制が弱い。
委員会形式の推進体制では,ややもすると,日常業務が優先し,推進体制が散漫になり易い。
以上,標準化阻害要因について述べたが,これに対する解決策を併記してまとめると,図-1の如くとなる。
これらの阻害要因を乗り越え,一気に標準化を強行することは,特に多種類の製品を対象とした場合,障害が多く,その前段階として「何等かの調整作業」と「魅力ある標準部品」を生みだすVE技法の必要性を感じた。
この結果,対応策として考案した技法が,以下に述べる「仕様平準化技法」である。